Experience
Ford Motor Company (2019-Present)
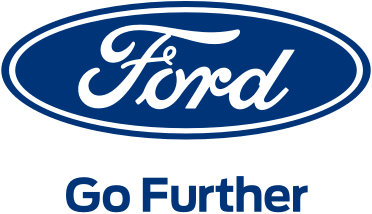
Sportscar Program Engineer - Ford Performance Motorsports
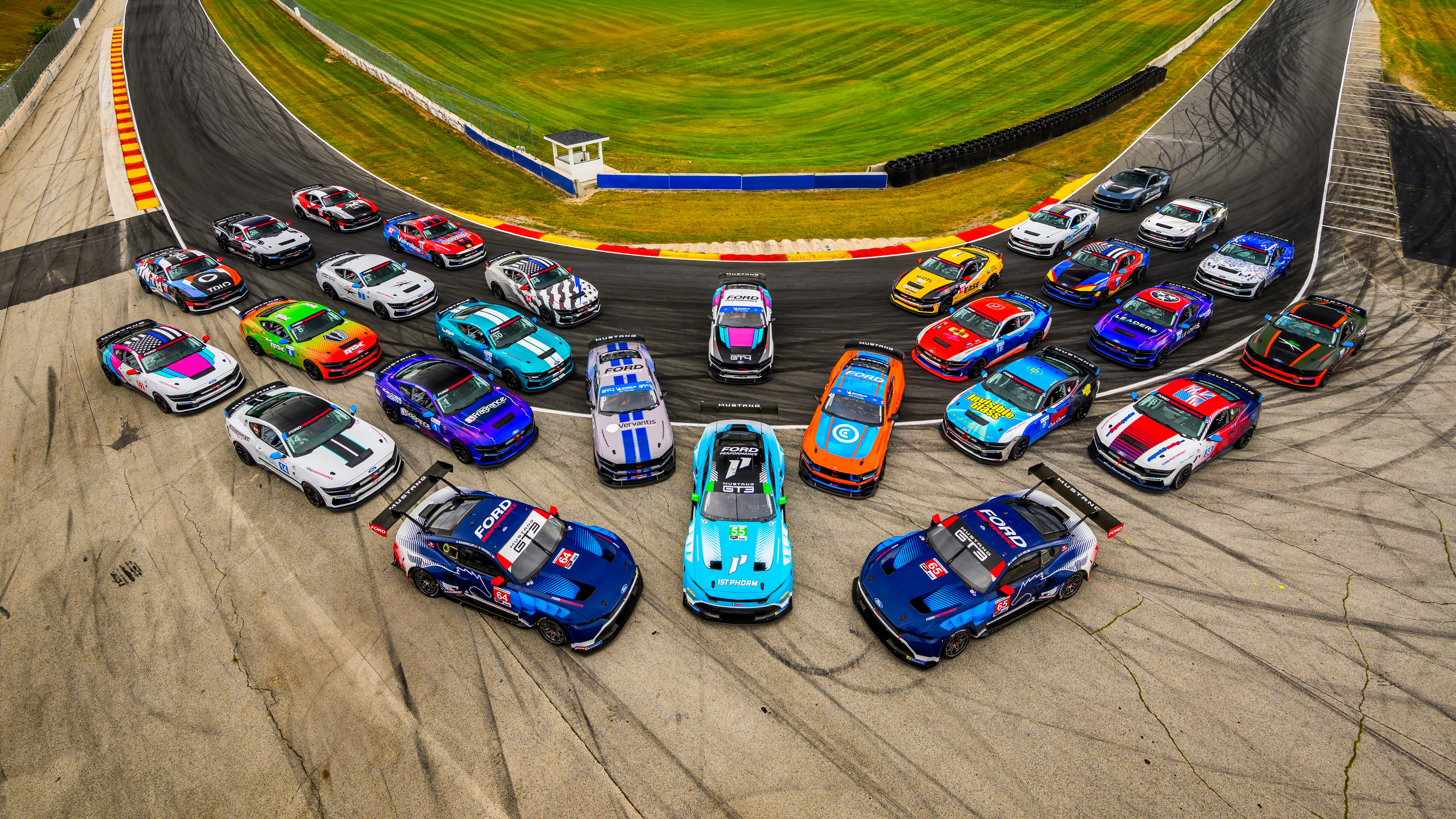
I currently work at the Ford Motor Company in Dearborn Michigan as a Sportscar Program Engineer in Ford Performance Motorsports. I primarily work on supports the GT3 and GT4 mustangs sportscar programs across various international series including the FIA World Endurance Championship in the LMGT3 class and IMSA with the GTD/GTD-PRO and GS classses.
Ford College Graduate Program
Iwas part of the Ford College Graduate Program which is a rotation program for recently graduated engineers that allows me to gain a wealth of experience in a variety of groups throughout Ford. My home group for this program is powertrain controls with rotations to support my future work in this department.
Rotations
- Rotation 1: Powertrain Control System Modeling & Software-in-the-loop(SIL)
- Rotation 2: Product Vehicle Team - F150
- Rotation 3: Advanced Powertrain Controls Development
- Rotation 4: Motorsports Calibraiton and Controls
Summer 2018
During the summer of 2018, I worked in Front End Systems Engineering within the Body Exterior department. I worked on the early launch stages of the MY2019 Ford Ranger and MY202 Ford Super Duty. During this time I worked on quickly resolving systems-level issues on a daily basis that occur during initial vehicle builds. I created a data collection and analysis tool that reports the fit and finish of front end components such as the bumpers and headlights. This tool decreased the time to collect measurements systematically by a factor of 3 and implemented automated statistical reporting which was not present before.
Key Achievements:
- Systems engineering intern for front end systems supporting new vehicle launch programs.
- Created system to track and report the progress of new build fit and finish with automation for checking against master specifications across various trim levels.
Summer 2016
During the summer of 2016, I work in Handles, Locks and Mechanisms group with the Body Exterior department. I helped analyze crash testing data for door latches to verify FMVSS requirements. I created a new tool that allowed for a 75% reduction in post-crash accelerometer data analysis time within MATLAB.
Key Achievements:
- Worked on new lightweight, fleet-universal crash safety device to protect against door openings in side-impact scenarios including CAD, simulation model and prototype and conducted crash test logistics and post-crash investigation relating to new latch assembly safety devices
- Created MATLAB based data analysis tools which became the standard use tool for the department in analyzing and dissecting accelerometer data.
Formula SAE - Illini Motorsports (2013-2019)
The highlight of my college career was participating in the Formula SAE competition, which is an international intern-collegiate competition where students design, build, test, and race a ground-up racecar. I owe all of the hands-on engineering knowledge that I learned prior to entering my formal career to the Illini Motorsports team and I encourage all student engineers to find a program similar due to the invaluable experience that it provides.
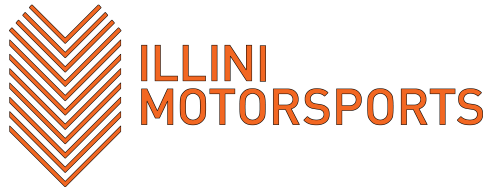
Team Captain
The peak of my time on the team was being the captain for two years, during which I was mananged a team of 50-100 student engineers across seven technical subsystems and two business and logisitcs subsystems with a ~$250,000 budget.
Achievements:
- Increased internal documentation database usage by 200%
- Increased number of key sponsors by 20%
- Peak International Ranking: 21st (out of 713 ranked teams)
- Peak United States Ranking: 5th (out of 713 ranked teams)
- Design Finalist at FSAEL
- 1st in the acceleration event at FSAEL
Composite Materials Design and Manufacturing Lead
My first leadership role on the team started in my third year as the subsystem lead for the newly formed Composite Materials Design and Manufacturing group.
Achievements:
- Reduced weight of composites aerodynamics package by ~25lbm (45% reduction over the previous vehicle) on 475 lbm vehicle for ‘15-‘16 competition season
- Increased sponsorship budget by 250%
- Managed and manufactured on first monocoque chassis for the team with specific design projects in designing and sizing lightweight and structural hardpoints, and overseeing testing and validation of selected ply schedules and structures
SpaceX
During the summers of 2015 and 2017, I worked at SpaceX in Los Angeles, California on both the new generation American crew capsule that will be taking US astronauts to the International Space Station, as well as supporting the manufacturing of the Falcon 9 rockets through friction stir welding.

Associate Engineer
I worked on supporting the component engineering group in friction stir welding that was used to manufacturing the rocket cores for the Falcon 9 rocket. This involved performed tensile and fatigue testing on welded specimens in both room temperature and cryogenic conditions. In this group, I also designed tooling that was used for non-destructive testing of rocket cores. These tests were performed using phased array ultrasonics and eddy current testing to verify the integrity of critical welds.
Key Achievements:
- Supported testing of fatigue specimens for flight-critical hardware in room temperature and cryogenic conditions through sample preparation, load frame testing, in-test measurement and analysis, and final compilation of results.
- Designed tooling to help support ultrasonic and eddy current inspection post-friction stir welding to increase rate and accuracy of inspection.
- Reviewed and analyzed manufacturing processes for friction stir welding and inspection with a result of increased throughput.
Internship 2015
My first internship after starting my college career was at SpaceX in the Dragon 2 Crew Capsule department. I worked in the composite structures group which was responsible for designing the critical primary and secondary composite structures on the crew capsule. Throughout the internship, I conducted an analysis using large vehicle-scale combined-load FEM models and I designed parts that interfaced with between various primary structures throughout the capsule. These designs were taken through the full engineering design process which involved extracting and collecting load cases, performing first order principles-based design, and then performed complex 3D analysis on these parts using various commercial FEA packages such as Ansys Mechanical and Siemens FEMAP. Throughout the process thermal, vibration, packaging and manufacturing constraints were constantly referenced to ensure a proper systems-level design. Additionally, I verified the designs of composite inserts and fasteners against continually updated load predictions. Finally, I worked on creating engineering drawings for the docking mechanism using standardized GD&T practices such as ASME Y14.5.
Key Achievements:
- Analyzed and designed primary and secondary metallic and composites structures to support a manned space capsule with efforts to reduce mass in high loading scenarios, and subsequently created technical drawings per GD&T and company specifications
- Refined and analyzed data from full vehicle fem models and performed data extraction and analysis to design load cases for physical testing of composite components